Enhanced Hydrogen Production from Biomass Gasification by In-Situ CO2 Capture with Ni/Ca-based Catalysts
Biomass and Bioenergy(2024)
摘要
Biomass is the important renewable clean energy. Compared to conventional technologies, biomass gasification experiences the problems of low hydrogen purity, low yield and high tar by-products. Coupling CO2 capture with biomass gasification for hydrogen production can promote the steam reforming and water-gas shift reaction to improve hydrogen production regarding both purity and yield. In addition, energy consumption of the reforming process can be reduced as well due to the heat release from CO2 adsorption. The application of Ni-based catalysts and CaO-based adsorbents faces problems such as poor resistance to sintering and easy deactivation. Here, biomass gasification experiments were conducted in a two-stage fixed-bed using pine sawdust as biomass raw materials. A range of Ni-Ce/CaO catalysts with different Ni loadings were synthesized using a sol-gel method. Characterization of these catalysts was carried out using techniques such as N-2 adsorption-desorption, X-ray diffraction, and field-emission scanning electron microscopy. Subsequently, a comprehensive investigation was conducted to assess the CO2 capture performance, catalytic activity and stability of the prepared catalyst. Results show that the Ni-Ce/CaO catalyst has the best performance at reaction temperature of 600 degrees C, Ni/Ce ratio of 2:1, and the steam flow rate of 5 mL/h. The optimum condition produced the lowest CO2 yield and the highest H-2 yield, which are 2.31 mmol/g and 12.8 mmol/g, respectively. The stability test of the Ni-Ce/CaO catalyst was also conducted, showing fluctration in gas concentrations initially during the first 5 h, then stablized for the remaining stability test.
更多查看译文
关键词
Biomass gasification,Hydrogen production,Process optimization,In-situCO2 capture
AI 理解论文
溯源树
样例
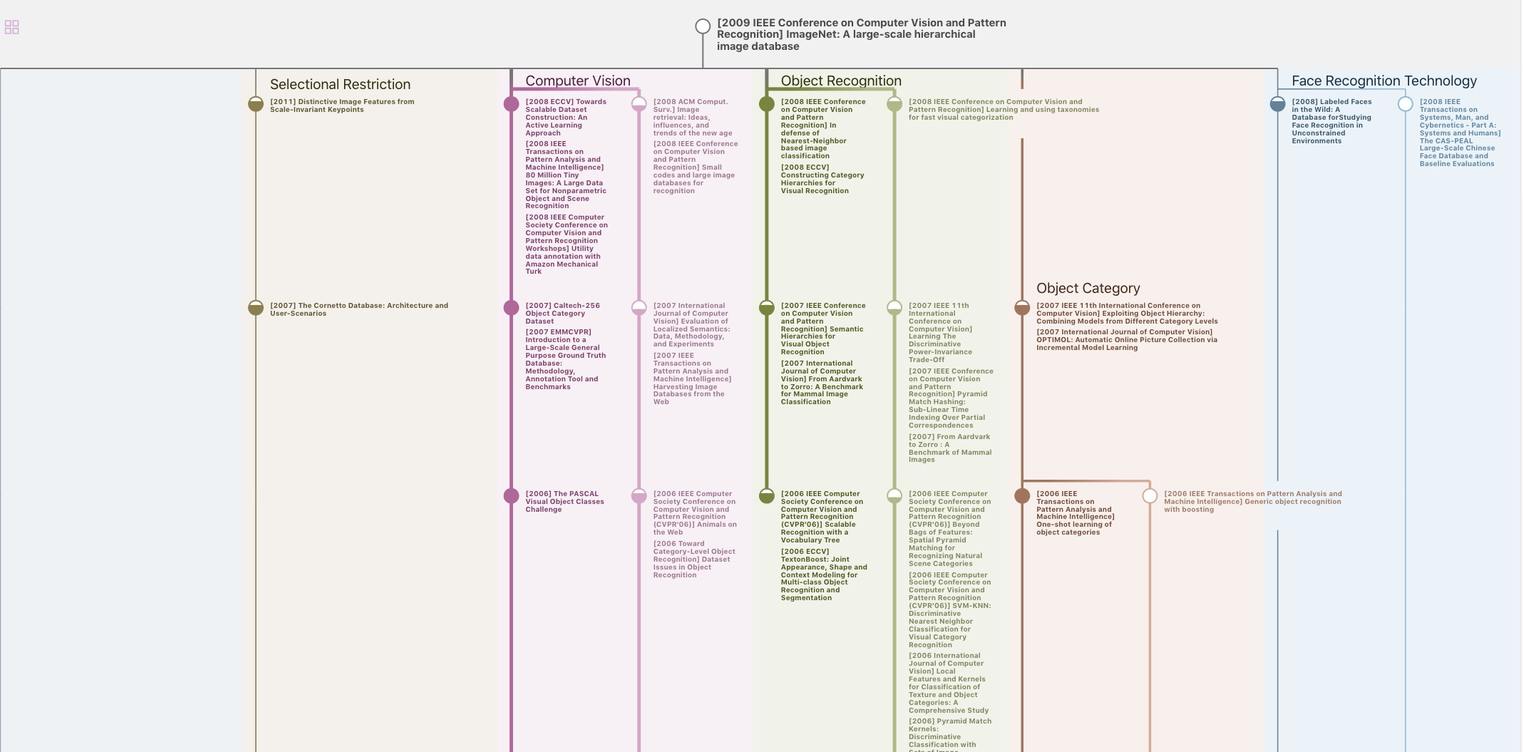
生成溯源树,研究论文发展脉络
数据免责声明
页面数据均来自互联网公开来源、合作出版商和通过AI技术自动分析结果,我们不对页面数据的有效性、准确性、正确性、可靠性、完整性和及时性做出任何承诺和保证。若有疑问,可以通过电子邮件方式联系我们:report@aminer.cn